AI powers BMW's vision for high-quality smart manufacturing
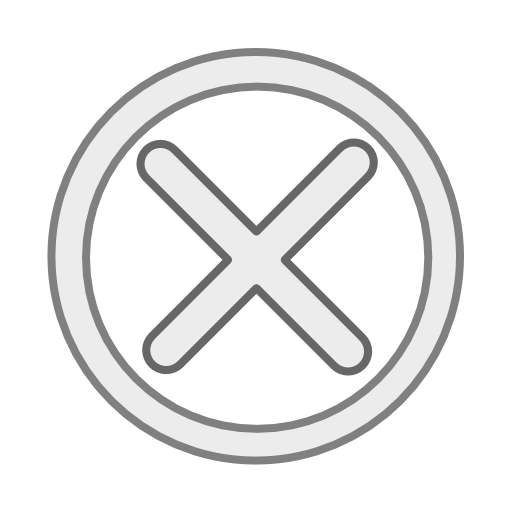
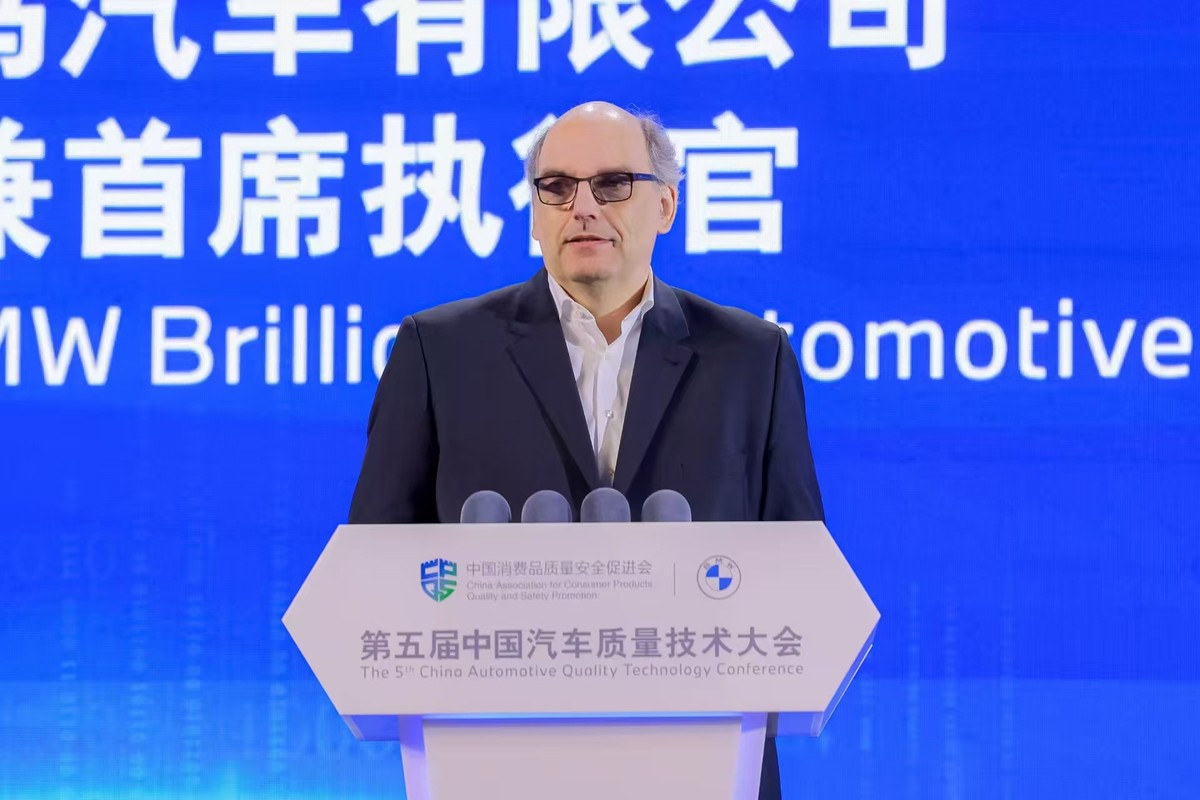
As the automotive industry undergoes a digital and electrified transformation, BMW is setting new benchmarks for high-quality intelligent manufacturing at its Shenyang production base, driven by advanced artificial intelligence technologies.
During the 5th China Automotive Quality Technology Conference, global experts gathered to explore how innovation, safety, and quality can converge in the next era of automotive development—with BMW Brilliance Automotive taking center stage.
Hosted on Thursday in Shenyang, a major industrial hub in Northeast China's Liaoning province, the conference brought together more than 600 delegates from leading automakers, suppliers, government bodies, and academic institutions.
Participants included representatives from FAW, Dongfeng, Huawei, CATL, Bosch, and top technical institutions, alongside senior officials from over 20 government departments.
During the event, delegates toured BMW's Shenyang production base—home to one of the world's most advanced automotive manufacturing operations.
With approximately 200 AI applications integrated across its operations, BBA has embedded artificial intelligence throughout the value chain: from predictive maintenance and visual inspection to R&D simulation and smart logistics.
These intelligent systems prepare the plant for the production of the Neue Klasse, BMW's next-generation vehicle architecture, while establishing a benchmark for China's shift from traditional to intelligent manufacturing.
"Quality is not for negotiation—not yesterday, not today, and certainly not tomorrow," said Franz Decker, president & CEO of BMW Brilliance Automotive.
"The Neue Klasse is not just a car—it's a revolutionary leap forward, and every component and system must meet our highest standards of excellence."
BMW's Shenyang production base has developed several industry-first capabilities, including a self-developed AI quality inspection system in the press shop and near-100 percent accuracy AI visual inspection in the paint shop.
AI is also being used in simulations to optimize battery thermal management and surface design in early R&D stages, accelerating development while improving safety.
Michele Mechiorre, senior vice-president of Technology & Manufacturing, emphasized: "Aligned with BMW Group's global quality benchmarks, our Shenyang base operates a rigorously validated system that exceeds industry standards. We aim to become China's No 1 premium manufacturer."
Looking ahead, the Neue Klasse presents new demands across production processes, workflows, and quality control.
BMW's response is its "zero" concept—zero defects, zero delays, zero waste—which permeates every step of the lifecycle.
In addition, BMW's R&D center in Shenyang houses nearly 30 dedicated test benches for GEN6 powertrain testing, along with the industry's first integrated EMC laboratory designed for intelligent connectivity validation.
Further advancing its local innovation strategy, BMW announced its partnership with Momenta to co-develop a China-specific ADAS earlier this week.
This system integrates AI large models and two decades of BMW safety expertise to deliver trustworthy, production-ready, and locally adapted intelligent driving experiences, said the carmaker.
BMW has also called on automakers to adopt a long-term approach, strengthen self-regulation, and safeguard the collective good of the industry.
Zheng Yuanhui, secretary-general of the Automotive Committee of the CACPQSP, stated: "The advancement of any technology should be premised on safety. BMW adheres to the bottom lines of safety and responsibility, playing a positive, exemplary, and leading role in the industry's high-quality development.
"Only by the entire industry jointly resisting cut-throat competition can we provide consumers with higher-quality, more reliable products and services, achieving high-quality and sustainable development," said Zhang.